Indirect-fired kilns are unusually important where direct-fired operation cannot be employed due to controlled heating, product contamination, etc. These challenges respond to niche applications of unusually high value.
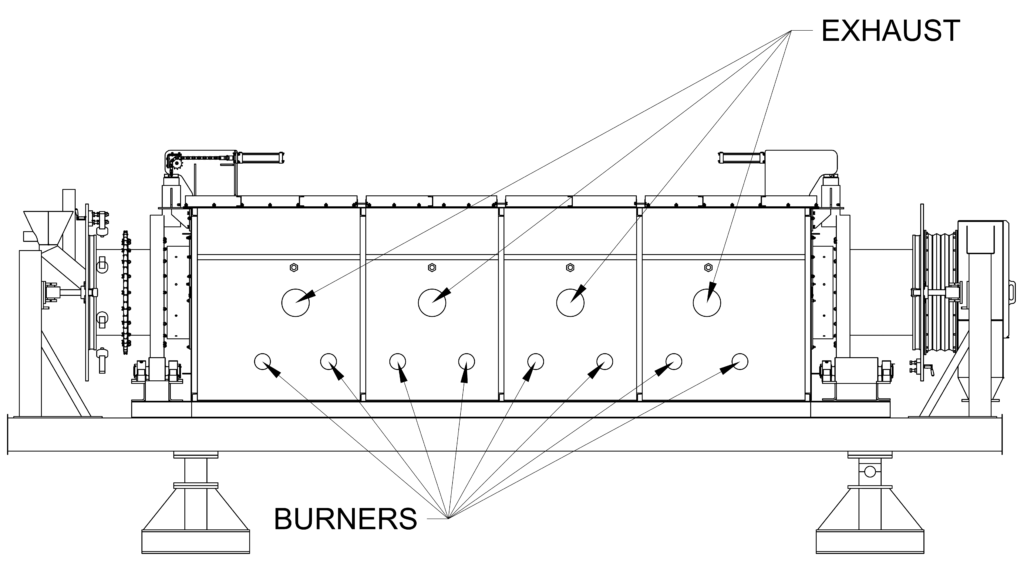
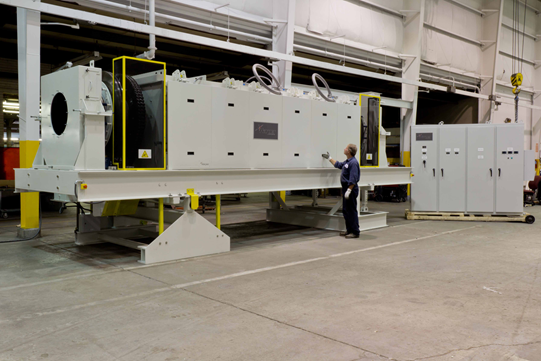
In the forefront of the indirect-fired kiln offering is Harper International, a reliable AlphaThermal collaborator. We have been privileged in having a cordial working relationship with Harper in the area of indirect kiln design for several applications including Ni-Co processing in China, design of a nickel briquette in South Africa, reduction of copper oxide to elemental copper in Germany, molybdenum ore reduction kilns, and metal-alloy kilns in the US. A typical design approach for a recent job may be summarized as including the following:
- Flue Design and Combustion Chamber Emissions
- Refractory Selection
- Heat Balance
- Miscellaneous Design Review or Questions
- Kiln direction of rotation
- Evaluation of bed fill fraction, fill angle, bed depth, and residence time using an in-house model
Addressing these via the use of an OpenFOAM computer modeling provided the optimum layout of burners, heating patterns, etc.
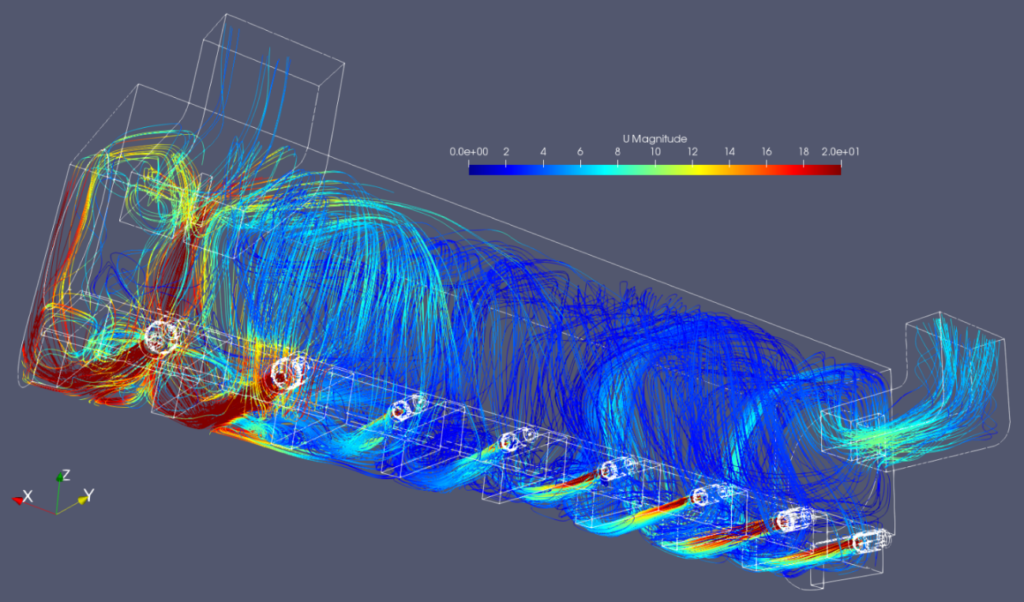
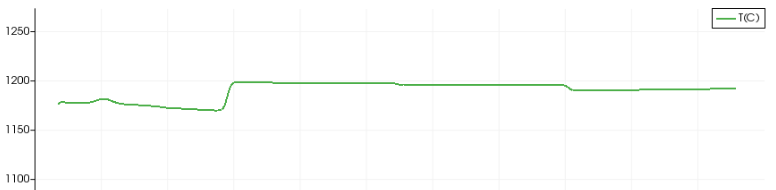
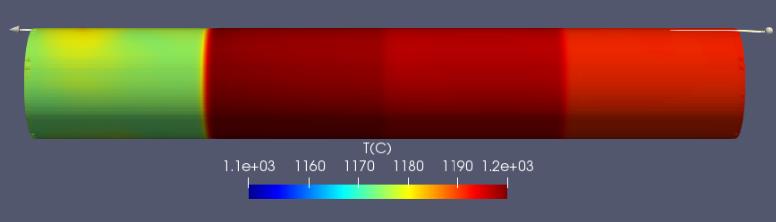
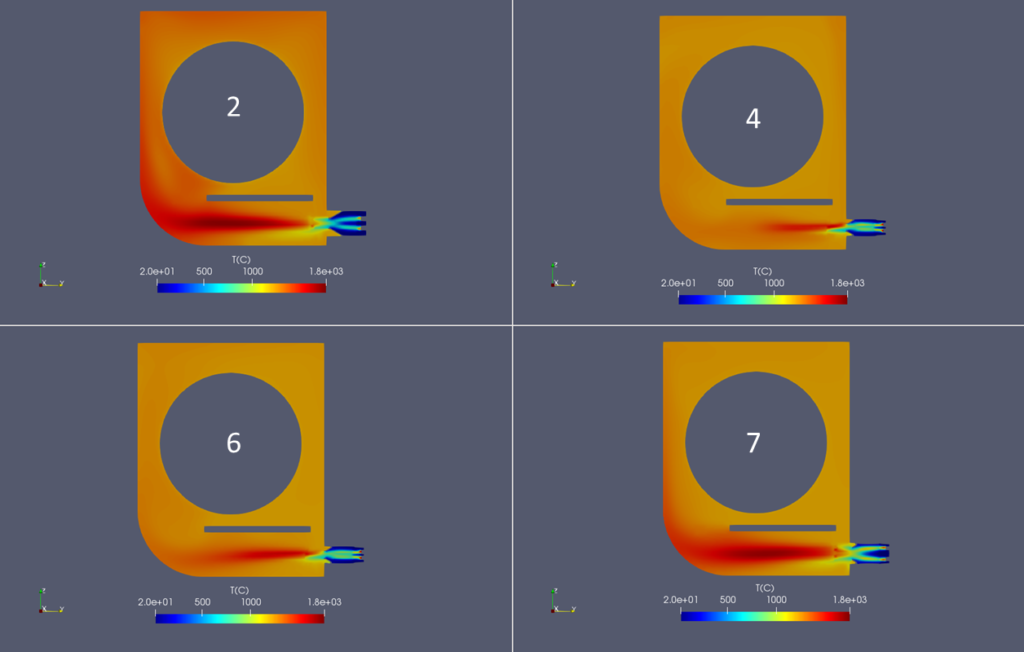