A lime kiln cooler required more air than needed for combustion to cool the product lime. One solution proposed by the plant was to discharge some of the air from the fire hood before it enters the kiln. It was anticipated that this air would be ducted off and then re-entered into the system at the back-end of the kiln.
Estimates showed that about 11000 lb/hr of air at 1100 F would have to be ducted to maintain an acceptable kiln back-end O2. AlphaThermal was charged to size the duct so as to ensure appropriate pressure drop and velocity were achieved that would minimize excessive dust settling.
Duct sizing Procedure:
The sizing was carried out by following duct design calculations. First a pipe size was selected and with the plant elevation and temperature, the properties of the conveying air and outside tube film air properties were estimated. The inside and outside air velocities were established from which the appropriate Reynolds numbers were computed. With the Reynolds numbers known inside friction factors were estimated using Moody Diagrams. Major and minor pressure drops were then calculated. The major DP was estimated using the desired tube length while the minor DP was based on the number of 90 deg and 45 deg bends required.
In order to include the complete effect of temperature, the tube was divided into several segments. For each segment the convective heat loss was calculated based on ambient conditions thereby allowing estimates of the segment’s exit temperature. At the same time the pressure drop across the segment was computed. The calculation was repeated for the next segment using the previous exit temperature as inlet temperature with the total pressure drop being the sum of all segments.
Selected Duct:
Our calculations indicated that:
1. The temperature drops quickly at about 5 deg per ft for the 200-ft duct attached to kiln #1 and about 4 deg for the 260-ft duct for kiln #2.
2. The pressure drop was appropriate for Schedule 40 pipe sizes equal or greater than 14-in.
3. Assuming that the minimum velocity required to prevent settling of dust (using coal analogy) is 12-15 m/s (about 3000 ft/min) 14-in schedule 40 pipe was selected be the optimum sizing for the job.
4. Another recommendation was to use a 16-in or 18-in pipe for the first 100-150 ft and a 14-in pipe for the next 50-110 ft should the pressure drop become problematic.
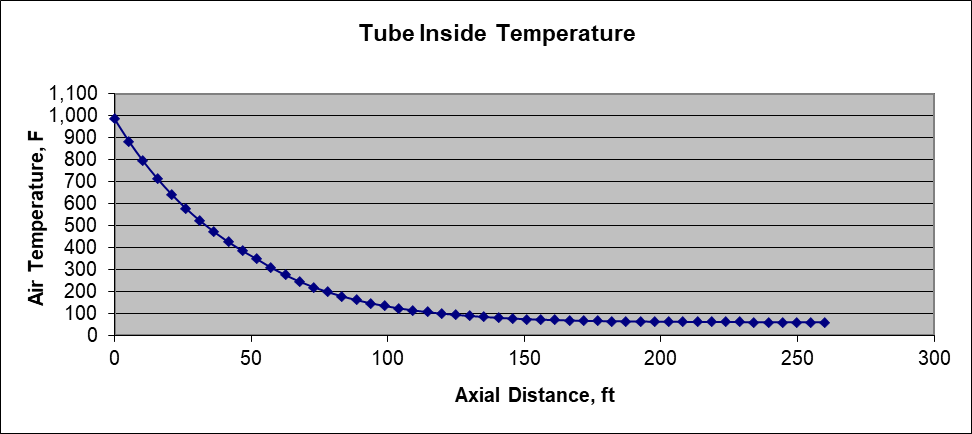
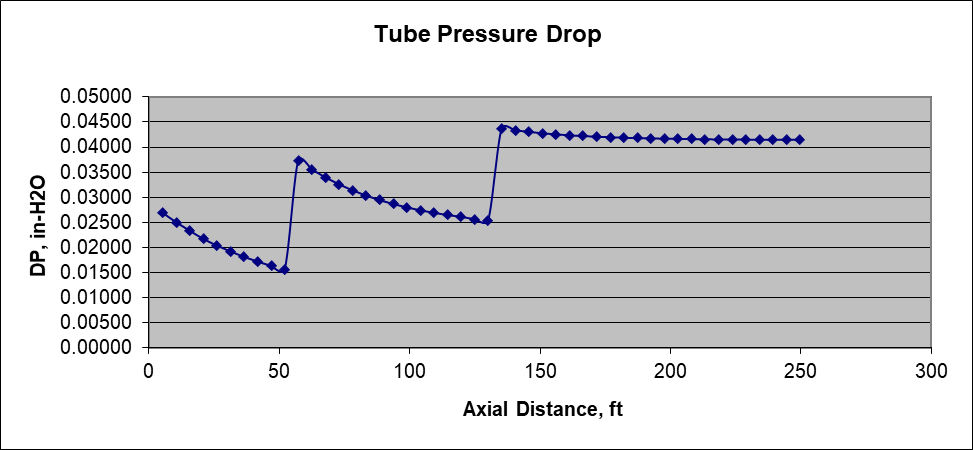
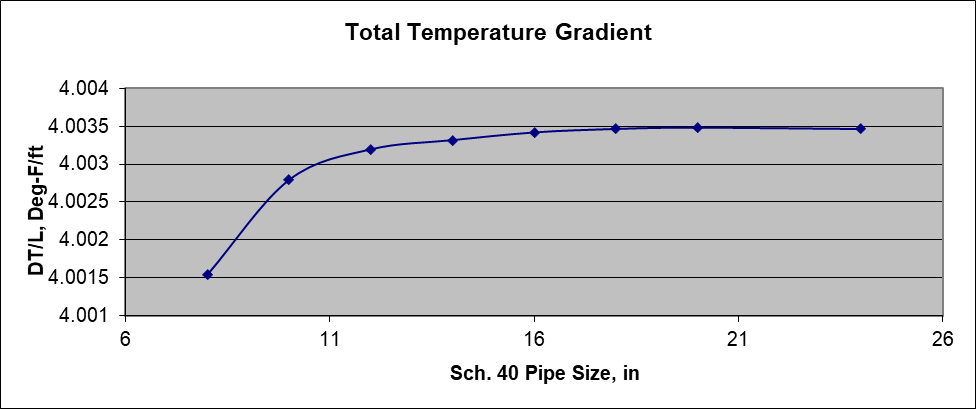